ABS(丙烯腈-丁二烯-苯乙烯共聚物)造粒机的工艺流程主要包括以下几个关键步骤: 原料预处理**: - 准备ABS树脂以及可能添加的各种助剂,如抗氧剂、阻燃剂、增韧剂、色母粒等。不同的应用场景对ABS性能要求不同,所以助剂的添加种类和比例也会有所差异。 - 对原料进行干燥处理,去除其中的水分。因为水分的存在会影响ABS的加工性能和产品质量,可能导致制品出现气泡、表面缺陷等问题。一般采用热风干燥机,在适当的温度(如80℃-100℃)和时间(数小时)条件下,使原料的含水率降低到合适范围(通常小于0.1%)。 配料混合**: - 根据产品的性能要求,按照精确的配方比例,将干燥后的ABS树脂和各种助剂通过计量装置进行准确称量。 - 把称量好的原料送入高速混合机中进行充分混合。高速混合机通过搅拌桨的高速旋转,使各种原料在短时间内均匀分散,确保后续加工中各成分的性能得以充分发挥。混合时间根据原料特性和混合效果要求而定,一般为几分钟到十几分钟不等。 熔融塑化**: ABS造粒代加工_ABS造粒代加工 - 混合均匀的物料通过上料装置输送至双螺杆挤出机的料斗。 ABS造粒代加工_ABS造粒代加工双螺杆挤出机的螺杆具有特殊的结构,通常采用啮合型同向旋转或异向旋转的螺杆设计。 - 在挤出机的机筒上设置多个加热区,通过电加热或其他加热方式使机筒内的温度逐渐升高,物料在螺杆的推动下向前移动,同时受到剪切力和摩擦力的作用,逐渐熔融塑化。不同区域的温度设置需根据ABS的熔点和加工性能进行精确调整,一般从加料段到机头温度逐渐升高,范围大致在180℃-250℃之间。 - 螺杆的旋转不仅推动物料前进,还对物料进行进一步的混炼和均化,使物料的各组分更加均匀地分布,消除物料中的温度和组成差异。
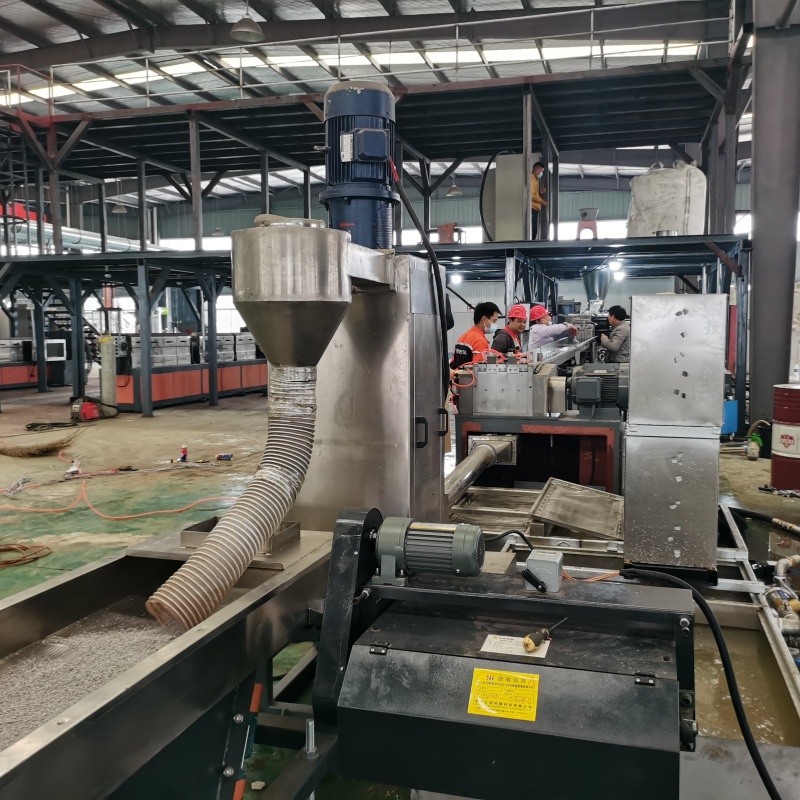
挤出成型**: - 经过充分熔融塑化的物料从双螺杆挤出机的机头挤出。机头内设置有特定形状的流道和模口, ABS造粒代加工_ABS造粒代加工物料通过模口时被挤出成连续的条状。常见的条状截面形状为圆形或近似圆形。 - 为了使挤出的条状物迅速冷却固化,通常采用风冷或水冷的方式对其进行冷却。水冷是较为常用的方法,通过将挤出的条状物引入水槽中,使其表面温度迅速降低,实现初步固化。风冷则是利用风机产生的气流对条状物进行冷却,风冷相对温和,适用于一些对水敏感或对表面质量要求较高的产品。 切粒**: - 冷却后的条状物料被输送至切粒机。切粒机的旋转刀具按照设定的长度将条状物料切成颗粒状。 ABS造粒代加工_ABS造粒代加工切粒机的刀具转速和进料速度需要精确匹配,以确保切出的颗粒大小均匀一致,满足产品的尺寸要求。 - 切粒过程中,为了防止颗粒相互粘连,通常会在切粒机中加入适量的润滑剂或抗粘连剂。
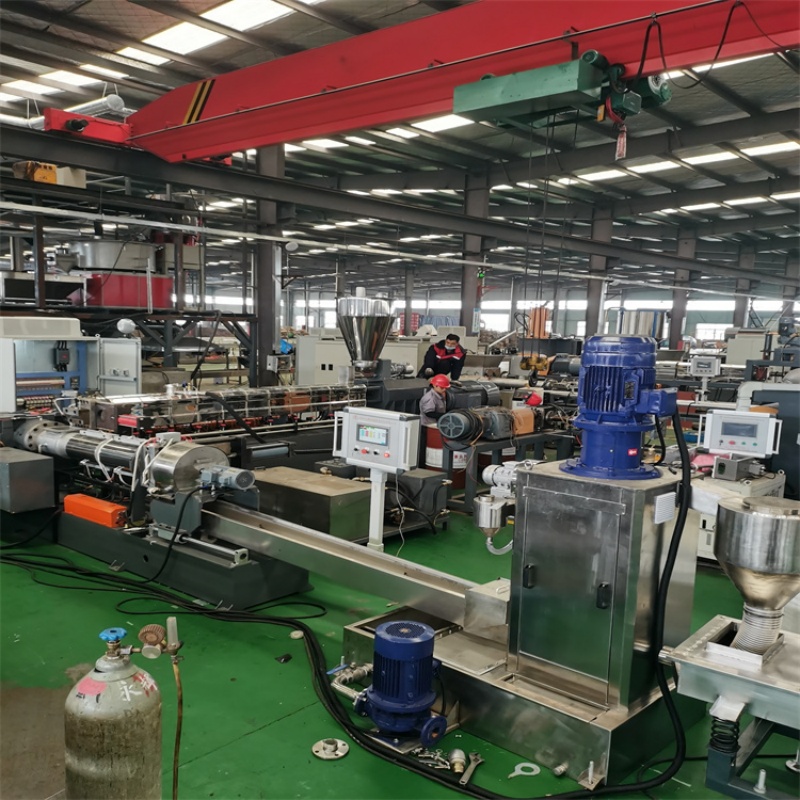
后处理**: - 切粒后的颗粒通过振动筛进行筛分,将不符合尺寸要求的颗粒(如过大或过小的颗粒)筛选出来,这些不合格的颗粒可以返回至生产流程中重新加工。 - 合格的颗粒可能还需要进行进一步的干燥处理,以去除在切粒和运输过程中可能吸收的水分,确保产品的质量和性能稳定。 包装入库**: - 经过后处理的合格ABS颗粒通过自动包装机进行定量包装,ABS造粒代加工_ABS造粒代加工一般采用袋装或桶装的形式。在包装过程中,会对产品进行标识,注明产品的名称、规格、生产日期、批次号等信息。 - 包装好的产品按照规定的储存条件存放在仓库中,等待发货或进一步的使用。 以上就是ABS造粒机的基本工艺流程,实际生产中可能会根据具体的产品要求和生产条件进行适当的调整和优化。